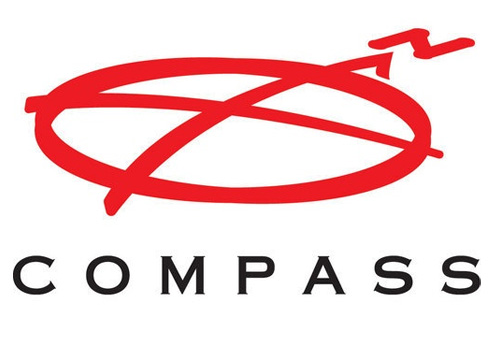
Compass Design
We design and engineer innovative products, intuitive interfaces and compelling brands for our clients.
Designs That Work
Brands That Sell
Compass has two locations; the main office and design center is conveniently located in Pleasanton, California near the major technology centers of San Francisco and San Jose. In addition, we have engineering and product development support in Tempe Arizona.
Pleasanton is at the intersection of Highway 680 and Highway 580. We have excellent transportation links. We are approximately 45 minutes by car from San Francisco, 35 minutes to San Jose and 30 minutes to Oakland.
Bay Area Rapid Transit (BART) has two stations in Pleasanton with service to Oakland and San Francisco.
We are served by three international airports; San Francisco, San Jose and Oakland. All three airports are less than a hour away.
If you would like to visit our Pleasanton office, arrange a meeting or need further information, please use the form below or call us directly – 925/462-3116.
Years Established
Completed Projects
Wireless Gateway for Confidential Client
California
Working with a tier one OEM supplier, Compass was brought in to help get a new wireless gateway product designed and ready for production. The end client had strong input into the design and features of the product.
This was projected to be a high volume – 2,000,000 to 3,000,000 units per year, so refining the mechanical details for easy and efficient production was critical. We worked with the contract manufacturer to insure the design would flow smoothly into production. Every detail, no matter how small, was reviewed and refined until the documentation package was released.
A clear prototype was built to help the entire development team see the details of the design.
Compass Services:
Industrial Design refinement, Mechanical Engineering, Prototype fabrication
Services
Complete product development? Yep, we can do that. Need some engineering help to get over a hurdle? You found the right place. Need to get your idea into production? We’re here to help.
From the initial research through to final production liaison, call on Compass to be your product development partner.
Click on any of the services below for further information:
Plan to succeed
Effective project planning and proper research is critical to the success of new product development efforts. Since we develop a large number of medical devices, user research is an especially important piece to the design development.
From the start of the project, we map out the performance requirements, usability strategies and product cost targets. It is also important where possible to identify component suppliers and production strategies for all major components to make the development run smoother.
Planning
Roadmap to success
Every product travels a journey. From the initial idea, through product definition, refining the design and proving the concept to finally delivering a finished product to your customer. For this journey to be successful, it is crucial to set a proper course and hit all the milestones.
At the beginning of the project, we’ll facilitate a project kick-off meeting to review and discuss the product goals, marketing targets including the corporate image, human factors for the product use, environmental requirements, regulatory agency approvals, material selection and manufacturing capabilities. By understanding these key project elements it helps to insure your project doesn’t veer off course and arrives to your customer on budget, on schedule and on target.
What else would you expect from a company named Compass?
Observation
Nothing like first hand experience
To get a better understanding of the project and the user’s experience, we watch, ask questions and listen to the product users or target audience. We’ve been in numerous operating rooms, asked teenagers about acne products and filmed users trying to figure out how to clear a jam on a copier. When possible, we roll up our sleeves, climb in and experience the product ourselves, as shown in the photo above.
Here, one of our designers is understanding the patient experience in the Imatron CT scanner. Body scanners can create feelings of claustrophobia in some patients and we wanted to get first hand knowledge. By getting on the patient table and going through the motions of a scan, the designer can see for herself what we could do to help minimize that sensation.
Competition
Know the enemy
It’s important to know the competition. Our staff will study what they are doing, how they implemented their solutions, and use that information to position our client’s product in the market. We look at the competitive products through the eyes of the target consumers by using the competitor’s product when possible. We research through traditional as well as online media sources.
Brainstorming
Diverge to converge
The goal of a brainstorming session is to generate, nurture and build on as many ideas as possible in a condensed time. To accomplish that, we bring together a diverse group of contributors – designers, engineers, human factors specialists, users, clients – and have them tackle the problem. We try to come up with as many possible solutions to the problem as we can and capture those ideas in quick sketches. The sketches are displayed for everyone to see and participants are encouraged to build on the ideas they see. The outcome is a wealth of new and creative problem solutions in a short time span.
Lifestyle Profiles
Who are these people?
Who is going to use the product? What are they like? What is important to them? These are some of the questions we ask when starting a new project. We want to intimately know who the customer is so we can craft the best product solution to meet their needs.
And the customer is not just that person who buys the product at the store. It may also include the service technician, the assembly person on the manufacturing floor and the marketing professional who is charged with selling the product.
For each “customer” we create a user profile that personifies their personal attributes such as likes, needs, capabilities and technical awareness. The staff then uses these profiles throughout the process to help judge their design solutions as the project moves forward.
The road to production starts here
Form and function. The user experience. Color and texture. Aesthetics. Usability. Marketability.
We think a product should be: Innovative Unique, inventive and original. Innovative products give your company a competitive edge. Intuitive Easy-to-use, positive and friendly. Making technology accessible to your customer. Desirable Inviting, alluring and intriguing. Creative design and engineering builds an appeal for your product. Manufacturable Cost effective, timely and appropriate. Products designed for quality production from the beginning.
Ideation
Sketch this
Most of our designers grew up sketching with a pencil and paper and it’s still the best way to quickly capture product concept ideas. No other medium gives the designer the speed and freedom to explore ideas better than sketching. For some projects, we will create hundreds of sketches looking at the form, colors, construction techniques and style before arriving at the final design.
We still sketch with a pencil and paper. And to keep up with the latest technology, we now also use tablet PCs with Alias Sketchbook Pro software, which allows the designer to draw directly on the computer screen, a “new school” approach to a traditional skill.
Human Factors
The connection between the product and the user
The term human factors encompasses a variety of man to machine interface elements. Some of the work is physical where we craft the design to fit the users body size, kinematic capabilities and strength. Other work deals with the cognitive ability of the user to understand how to use a product, user interface design and menus. And finally there is organizational design where the product and the entire work structure is studied and optimized.
In the example shown above, we’re setting the anthropometic parameters for a medication delivery cart design project.
Soft Models
3D sketching for the design staff
We like models. Our staff thinks of them as 3D sketches, a way to work out the forms and shapes for a new design with their hands. Sometimes they’re rough, maybe even crude to quickly evaluate a design direction. This way in a matter of hours or a few days we can review the design and use the information to keep the project moving. This saves our client time and money.
At other times, like the urethane foam model above for a dermatology laser, they are more carefully finished as part of a later stage appearance presentation.
We make these models in one of our two, in-house model studios using foam core board, plastic and urethane modeling foams.
Appearance Models
Looks like the real thing
Appearance models show the final appearance of the product before the production parts are ready. They can be used in trade shows, marketing collateral and to show the product team the direction of the final design. Some models we make in-house and others we use our development partners for a specific expertise. Over the years we have made models that are small enough to fit into your mouth as well as large, full-scale capital equipment projects.
The OUR Medical model shown above was used extensively for trade shows. Since the real product weighed 44,000 lbs. (yes, 22 tons!), this full size foam and fiberglass model was their only choice on the trade show floor.
Rendering
Photorealistic imagery
Sometimes, a hand sketch isn’t polished enough and building a physical model takes just too much time or money – that’s where a computer rendering really shines. Not only does the product image convey realistic textures and colors, but it can be placed into real life photo environments for focus groups and marketing feedback.
BodPod wanted to see their product before the tooling stage was started and they wanted to be able to show their customers the upcoming product. The rendering shown above was done in PhotoWorks, an add-in module to SolidWorks.
Where the rubber meets the road
It’s one thing to create a beautiful aesthetic design but another to be able to take that design and engineer it for production. At Compass we have a talented and experienced mechanical engineering staff to get the job done. They are experts in 3D CAD design, our preferred software is SolidWorks, and we use PDMWorks for file management. Our experience includes:
- Mechanism development.
- Complex CAD surface modeling.
- Sheetmetal design and fabrication.
- Design of tooling ready, injection molded parts.
- Materials and process technologies.
- Design for assembly and cost reduction.
- Green materials research and design.
- Vendor qualification and sourcing.
Concept
Build it, try it
This is where the mechanical engineer starts to piece together the foundation for the product design. Parts are put together with tape, hot glue and clamps to quickly try a variety of configurations for the design.
The photo above is of a light source for laboratory equipment and the engineer is looking at the placement of the fan to cool the light source.
Refinement
Dial it in
By the refinement phase we’ve got the basic configuration for the product and we’ve done enough development to start focusing in on the details of the design.
A good example is the Nektar drug delivery device. It uses a hand operated air pump to create air pressure for the device. One of the challenges was to design a handle that was comfortable for a large hand as well as a small hand that could effectively be used by someone with weak hands. We created the model shown above where we could attach different handle parts to try different designs before going to production.
CAD
No more pencil and paper
The mechanical engineering world revolves around the CAD system. Where the engineer used to detail the final design on a drafting table with sheets of vellum and graphite pencils, it’s all on screen today. We work in SolidWorks, ProENGINEER and Creo software packages.
And we have some of the best engineers in the business. We’ve won industry awards, been featured in CAD magazines and SolidWorks put one of our designs on their owner’s manual cover a few years ago. They’re good.
.
Analysis
Pressure packed
For some projects, we conduct an analysis of the design before any parts are made. In the example above, we used Nastran finite element analysis (FEA) software to investigate the loading on a vacuum lid design. By putting the design through a simulated test like this, we can see if there are any areas where the part needs strengthening or where we can reduce the material and still achieve the desired results.
Test & Evaluation
Test till you drop
For some mechanical devices and mechanisms, we put them through a battery of internal tests to see if the design can stand up to the requirements in the market.
That spinning blur in the middle of the photo above is a cam surface that activates the handles on a surgical device as it spins around. This particular unit has the capacity to hold three devices so we can test more units in the same amount of time.
Electronic arts
The electronic design team’s primary skill is the development of sophisticated and imaginative electronic circuits and embedded software systems. Design specialties include:
- Wireless data communications (Bluetooth and conventional AM/FM RF).
- Instrumentation and signal processing.
- Control systems.
- Embedded software for a variety of programmable devices including Motorola, Microchip, Atmel, Xilinx and Altera.
- Materials and process technologies.
- Design for assembly and cost reduction.
- Vendor qualification and sourcing.
The designs are created using primarily Protel DXP although the team also has experience with Mentor Graphics and Cadstar for PCB design. Software code is primarily written in ANSI-C but we also offer assembly code for various product families as well as Pascal and C++.
Concept
Finding a solution
Once the engineer has made a preliminary design on paper, the initial electronic concept design is often built up using either a breadboard or plug board as shown above. This allows the electrical engineer the freedom to experiment easily while testing out the design. A variety of electronic systems may be prototyped by using breadboards, from simple small circuits to entire CPUs. Of course, complex circuits can become unmanageable on a breadboard due to the large amount of wiring necessary. These more complex circuits are often “breadboarded” on the computer using simulation software.
Circuit Design
Electronic CAD
Once the concept circuit has been proven the next step is to bring the design into the CAD program where it can be prepared for the prototype build. The preferred software is Protel DXP but the team also has experience in Mentor Graphics and Cadstar.
Software
The window to the product
Software is what brings the product alive, gives it character and allows the user to interact with it. The design of a user interface allows the user to provide input into the system and interpret output from the system. To a large degree, it is a key element to the experience of using the product.
At Compass we use a collaborative approach to the user interface design bringing together human factors experts, graphic designers and the software code writers to work through the design and implementation of the interface.
Test & Evaluation
Running them through their paces
All through the electronic design process we test, revise, and test again. Our internal lab has all the equipment necessary to evaluate the design and test the functionality before going to production.
First impressions
As with any development process, prototyping the design is vital to the success of the product. This is where all the parts come together and the team can finally view the entire assembly. Often the prototyping phase will uncover areas where the design may be improved through some redesign or alternative component selection. The prototypes are also used for the initial regulatory agency compliance testing and other test procedures. They also allow us to conduct user feedback sessions gathering valuable information to be incorporated into the final design.
Part Fabrication
Cut away
The start of the prototyping phase is to fabricate the parts of the design. To do that, we utilize a variety of prototyping methods including CNC and hand machining, rapid prototyping directly from the CAD files, metal forming and welding, castings and various finishing techniques. Where possible we use the same material as the production unit to give more realistic and repeatable test results.
In the photo above, the front bezel for the Reliant product is being machined.
FDM (Fused Deposition Modeling)
Instant gratification
A few years ago we added a Dimension FDM (Fused Deposition Modeling) 3D printer to our in-house capabilities. The advantage over a SLA type printer is the FDM process uses ABS plastic as the base material giving parts that are stronger and more resistent to warping and deforming in heat. These parts are perfect to verify CAD data and can be finished as an appearance model.
We think there is a big advantage to having this printer at Compass. We have complete control over the build, we can set our own priorities based on the client’s schedule and we can monitor the build remotely via the internet. Another bonus – we can keep your project confidential.
The Dimension specifications are:
- Maximum build size per part is 8.00″ x 8.00″ x 12.00″ (200 x 200 x 300mm). We can combine parts to create larger models.
- The material is ABS engineering resin, various colors are available.
PCB Fabrication
Try it out
At facilities in Northern Ireland we can fabricate prototype and limited production PCB assemblies. Capabilities include; electroplated PCB fabrication, reflow SMT assembly, and various manual soldering stations. PCBA testing is carried out using a range of in-circuit test equipment and functional test equipment.
Painting
Give it a fresh coat
We offer a variety of painting, graphics application and finishing options. We can apply paint finishes from smooth and glossy to rough and weathered. In addition we can apply product graphics for a realistic appearance.
Assembly
Put it all together
The final act of the prototype phase is to assemble the parts and test the entire design against the specifications. Often this results in a short run of 3 to 9 sets of parts that are used in limited trials to gather feedback from real users. In some cases these units are also used for regulatory agency submission.
In the photo above the technician is assembling the Reliant Fraxel laser system for clinical trials. The covers for these prototypes are urethane castings with a sheet metal internal chassis.
Sell millions!
In this phase we finalize the documentation, provide production quotes, manage the tooling and initial assembly process and deliver products ready to sell. We’re thinking about the production phase all the way back in the very early concept development. This way we can design a product that not only has a desired appearance but one that flows smoothly into production. The photo above shows the Rainin E4 Charging station ready for final packaging.
Quoting
Finding the best partner
The quoting and vendor selection process usually begins early in the project with Compass researching and identifying a short list of qualified partners, usually both domestic and offshore. As the design files move through the process, we send quote packages for initial cost estimating as well as for feedback from the vendors to the Compass design team. This dialogue with select partners helps to refine the design for efficient production capabilities and supplies the team with the latest cost, component availability and materials information. That way we can help guide our client to the best decision for their unique needs.
Product Support
The final touches
Getting the product designed, engineered and into production is our primary focus but we’re often asked to provide additional product support. To complete the journey we offer the following services:
- Logo design.
- Product graphics.
- User/Quick reference guides.
- Packaging.
- Trade show displays.
By coordinating the entire product visual experience, we can create a complete image for your product.
Documentation
A complete package
Documentation of the design is the important, final step in the design process. We provide full documentation, both 2D drawings and 3D CAD files for the mechanical parts and Gerber files for electronics and the code for software. We also prepare a complete Bill of Materials for mechanical and electronic components.
First Article
Check it twice
First article inspection is our chance to check the tooled parts for the first time. Usually the vendor provides a first article report and we do our own checking of the part in-house. If needed, we may also send the part out for independent verification using one of our qualified suppliers.
Our Clients
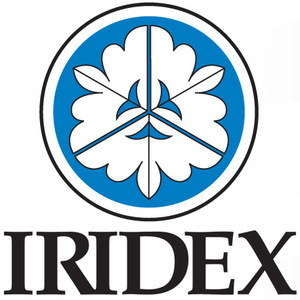
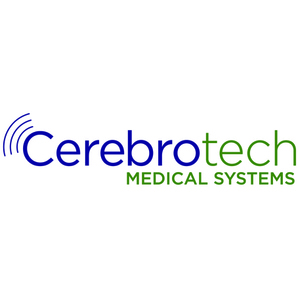
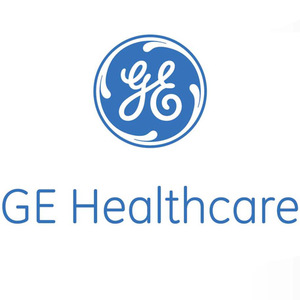
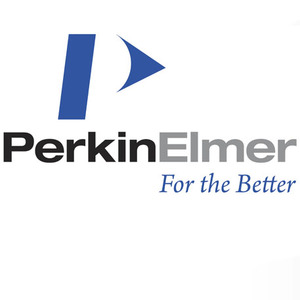
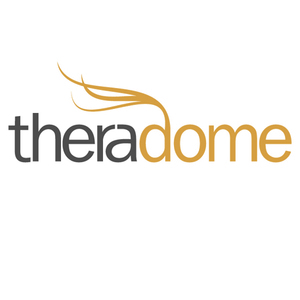
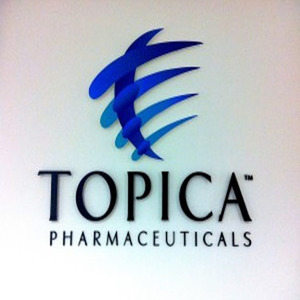
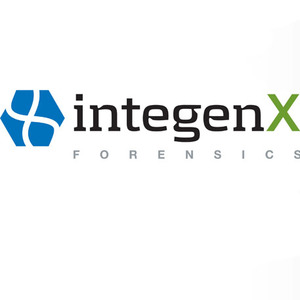
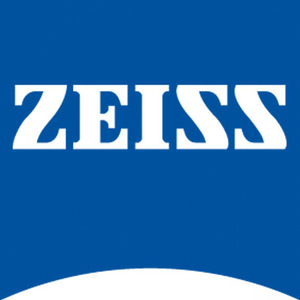
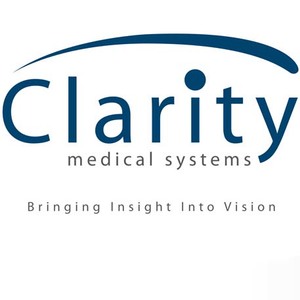
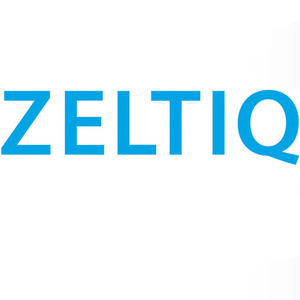
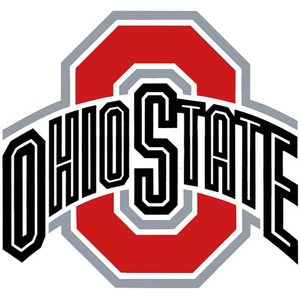
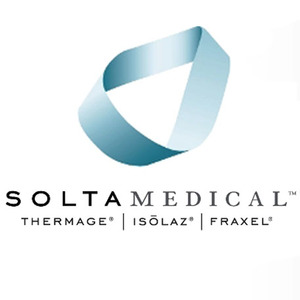
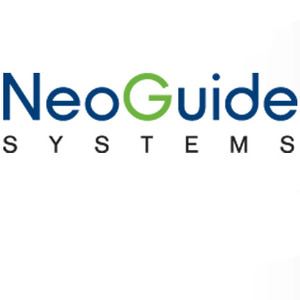
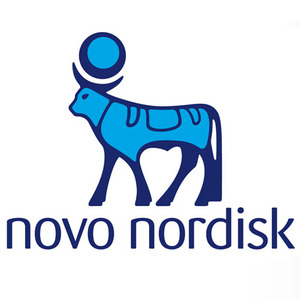
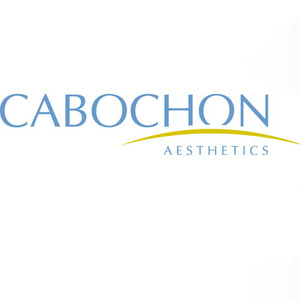
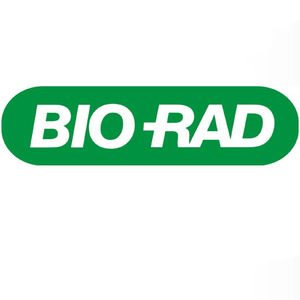
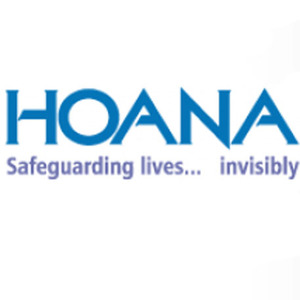
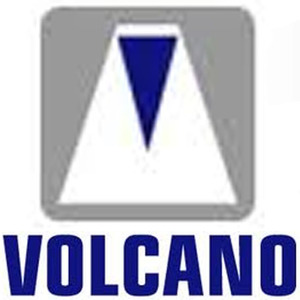
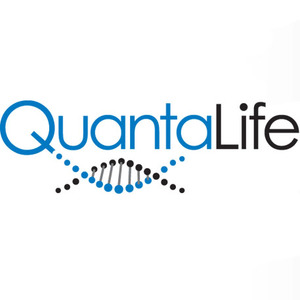
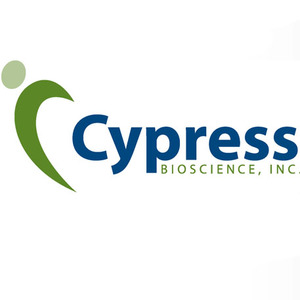
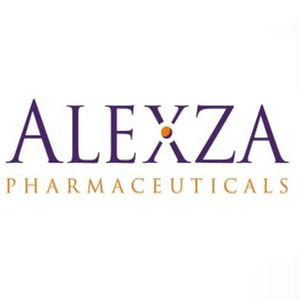
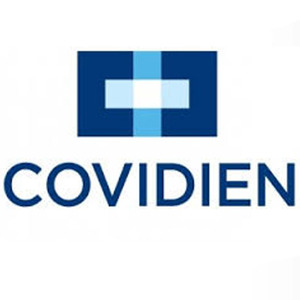
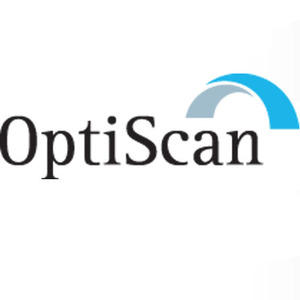
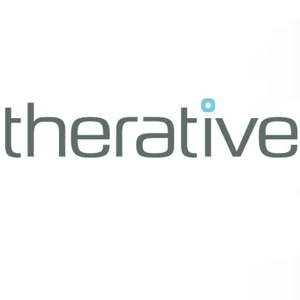
FAQ’s
Who, what, why, when, where & how?
No two projects, or for that matter, clients are alike. We’ve worked with one person, entrepreneurial start-ups and huge, multi-national corporations. Some just want a few sketches to get going while most ask for a complete development program – soup to nuts. The following are some of the more common questions we get asked about us and our services.
What do you mean "Designs That Work, Brands That Sell?
We think that phrase captures our philosophy perfectly. We create designs that work. They work in the market by being innovative, creative and unique. They work for the customer by being easy to use, friendly and a positive experience. And finally, they work on the manufacturing floor by being cost effective, timely and using appropriate materials and technology.
And we create brands that sell. It’s not enough to simply create a manufacturable design. the design must be compelling to the customer and entice them to choose one product over the other. The competition in any market is tough, make sure you choose a firm that can help you win the battle.
What if I only need a few services?
That’s not a problem. We can tailor our services to just what you and your company needs. We understand that not every client needs a complete development program and we’re happy to help those that just need a little help.
How are projects structured?
Our typical, full service project is broken into four primary phases; research, design, prototypes and finally, production. The research/design phase is when we learn about your particular idea, research the market/users and develop the basic functional foundation for the product. In the design phase, we build on the foundation with industrial design, mechanical and electronic engineering. We build prototypes next, test them and refine the design as needed. Finally we prep the product for production, manage the tooling process, conduct first article inspections and get the production line moving.
What software do you use?
For the 2D design side, we use: Illustrator, Photoshop, Alias Sketchbook Pro and Vellum Graphite. For the 3D engineering side, we use SolidWorks and ProEngineer/Creo as our primary platforms. We also use PDMWorks for document control.
Do you work with entrepreneurs?
Yes, many of the projects we have on this site were brought to us by entrepreneurs. Some projects are not a good fit for us but we’d be happy to talk with you. We’ll always give you straightforward advice.
How do programs get started?
We start with a conversation about your goals and how we may help you reach those goals. It’s important that we feel comfortable with each other and our philosophies are in sync. If everything is working out, we’ll prepare a proposal showing the plan for your project, deliverables, dependencies and schedule.
Sounds good, what's next?
The first step is to get in touch with us. To get the ball rolling, give Curt Anderson a call, his direct line is 925/485-1071
FREE ESTIMATES
Established in 1989, Compass Design provides a full range of product development services; research, industrial design, engineering, user interface, prototype fabrication, production management, documentation and low volume production.
We are best known for our work in medical devices though we have create successful, award-winning products for business clients, consumer projects, sporting goods, toys and industrial equipment.
COMPASS Product Design, Inc.
1061G Serpentine Lane
Pleasanton, CA
94566 USA
925/462-3116